Trong các quy trình tiệt trùng bằng VHP (Vaporized Hydrogen Peroxide) tại phòng sạch, việc kiểm soát nồng độ H₂O₂ là yếu tố then chốt nhằm đảm bảo hiệu quả diệt khuẩn mà vẫn đảm bảo an toàn cho thiết bị, sản phẩm và người vận hành. Vậy đâu là mức nồng độ lý tưởng để Pass Box khử khuẩn hoạt động hiệu quả mà không gây nguy cơ tồn dư hóa chất
- 1. Tổng quan về công nghệ khử khuẩn VHP trong Pass Box
- 2. Nồng độ H₂O₂ bao nhiêu là an toàn theo tiêu chuẩn quốc tế?
- 3. Cách đo và giám sát nồng độ H₂O₂ sau khử khuẩn
- 4. Quy trình xả khí và đảm bảo an toàn sau chu trình VHP
- 5. Rủi ro nếu nồng độ H₂O₂ vượt ngưỡng cho phép
- 6. Khuyến nghị vận hành và thiết kế Pass Box khử khuẩn VHP an toàn
- 6.2. SOP vận hành rõ ràng, chi tiết
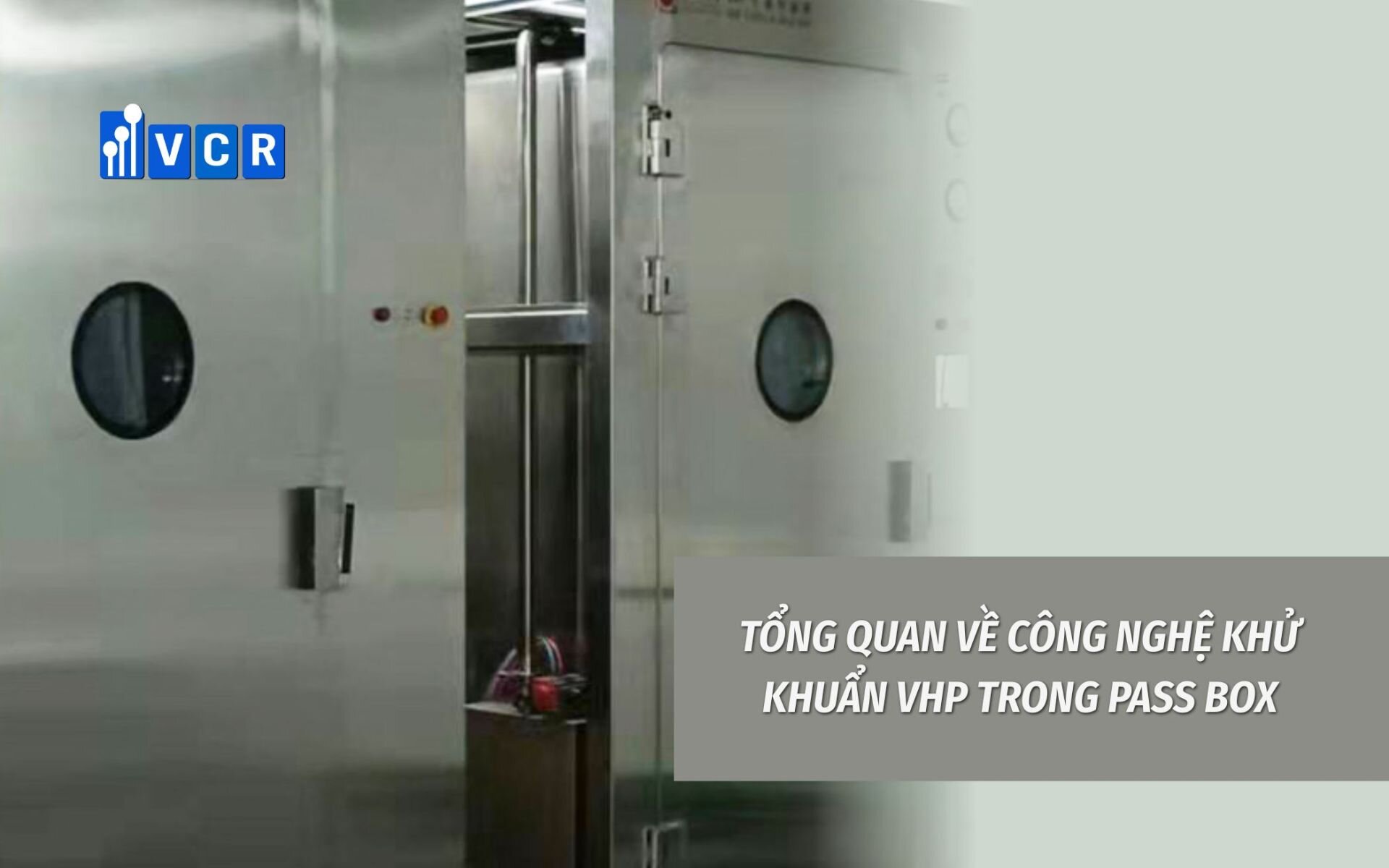
1. Tổng quan về công nghệ khử khuẩn VHP trong Pass Box
1.1. VHP là gì?
- Isolator vô trùng
- Phòng kiểm nghiệm vi sinh
- Dây chuyền chiết rót thuốc tiêm
- Và đặc biệt là trong Pass Box – nơi chuyển vật tư giữa các khu vực có chênh lệch cấp độ sạch.
1.2. Cấu trúc và nguyên lý hoạt động của Pass Box VHP
- Buồng kín inox (thường là 304 hoặc 316L)
- Hệ thống tạo và phun hơi H₂O₂
- Quạt tuần hoàn không khí bên trong buồng
- Đèn UV hỗ trợ hoặc cảm biến nồng độ H₂O₂
- Cơ chế interlock 2 cửa để ngăn mở đồng thời
- Hệ thống xả khí sau khử khuẩn (aeration)
- Pre-conditioning: ổn định nhiệt độ, độ ẩm và áp suất trong buồng
- Injection: bơm và hóa hơi H₂O₂ vào buồng, đạt nồng độ khử khuẩn mục tiêu
- Dwell: giữ nồng độ trong khoảng thời gian xác định (thường 10–30 phút) để tiêu diệt vi sinh
- Aeration: xả khí, làm sạch buồng, đưa nồng độ H₂O₂ trở về mức an toàn trước khi mở cửa
1.3. Vì sao cần kiểm soát nồng độ H₂O₂ sau khử khuẩn?
- H₂O₂ là chất oxy hóa mạnh, có thể gây kích ứng da, mắt, đường hô hấp nếu hít phải ở nồng độ cao.
- Theo nhiều nghiên cứu, ngay cả khi ở mức thấp (1–2 ppm), H₂O₂ vẫn có thể gây ho, cay mắt và khó chịu cho người thao tác nếu tiếp xúc thời gian dài.
- Đặc biệt trong các nhà máy GMP, nếu không kiểm soát tốt nồng độ H₂O₂ còn dư, Pass Box có thể trở thành nguồn phát tán hóa chất ra môi trường sản xuất.
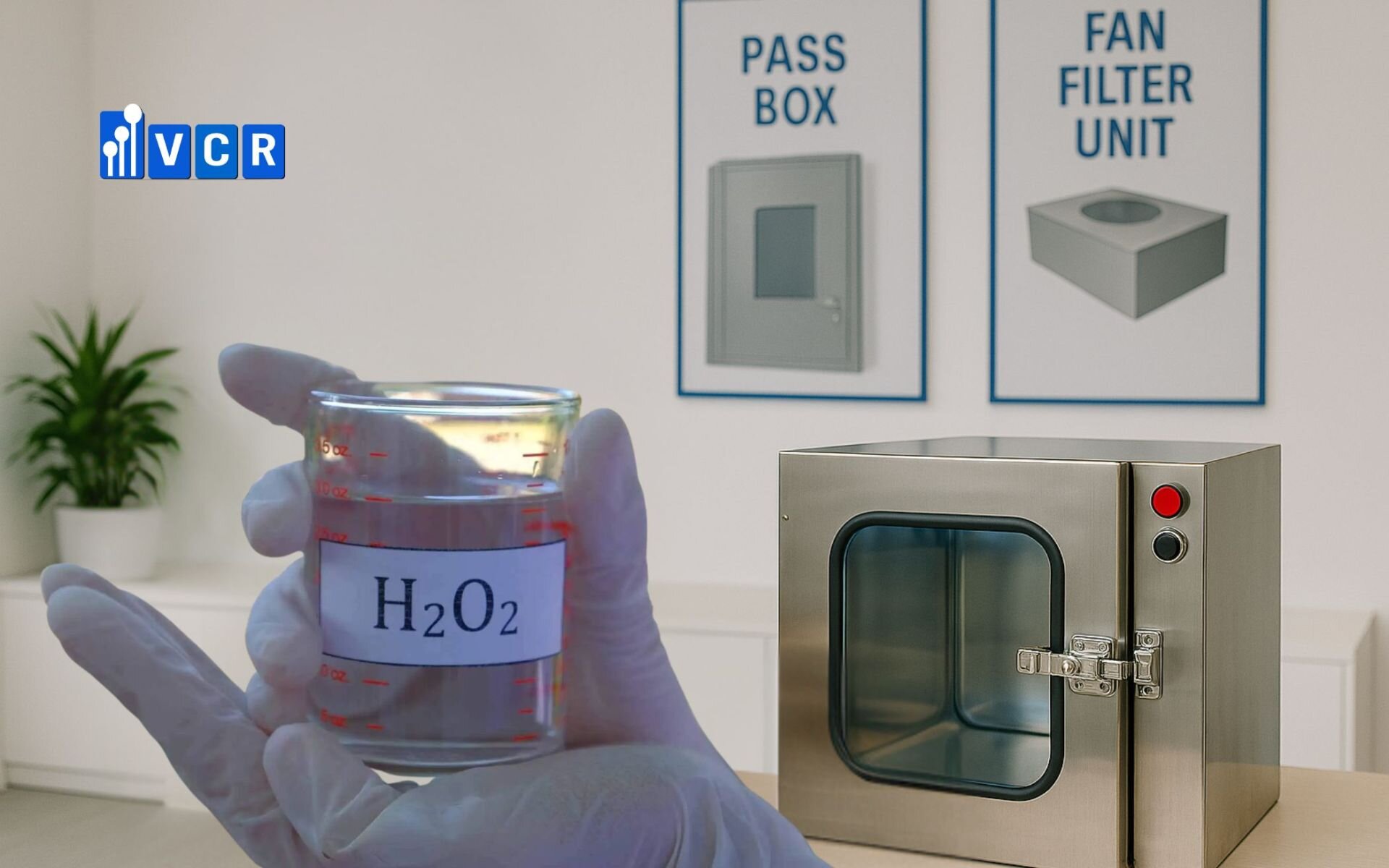
2. Nồng độ H₂O₂ bao nhiêu là an toàn theo tiêu chuẩn quốc tế?
2.1. Giới hạn tiếp xúc theo các tiêu chuẩn lớn
Tổ chức / Hệ thống | Giới hạn cho phép (TWA – 8h) | Ghi chú |
OSHA (Hoa Kỳ) | 1 ppm | PEL – Permissible Exposure Limit |
ACGIH (Hoa Kỳ) | 1 ppm | TLV – Threshold Limit Value |
NIOSH (Hoa Kỳ) | 1 ppm | REL – Recommended Exposure Limit |
EU / ECHA | ~ 1.4 mg/m³ (~1 ppm) | Áp dụng tương đương các hướng dẫn OSHA/ACGIH |
WHO / GHS | Cảnh báo: gây hại hô hấp, mắt… | Không khuyến nghị tiếp xúc trực tiếp >1 ppm |
2.2. Ý nghĩa của giới hạn 1 ppm
- 1 ppm = 1 phần triệu theo thể tích (1 thể tích H₂O₂ trong 1 triệu thể tích không khí)
- Đây là ngưỡng an toàn tối đa được phép tiếp xúc trong 8 giờ liên tục
- Trong phòng sạch hoặc Pass Box: mức H₂O₂ tồn dư cần xuống dưới 1 ppm trước khi mở cửa để đảm bảo không gây hại cho người thao tác
2.3. Tại sao 1 ppm là "ranh giới đỏ" trong GMP?
- Dư lượng H₂O₂ cao không chỉ ảnh hưởng sức khỏe nhân sự, mà còn:
- Làm oxy hóa thiết bị, inox, gioăng cao su
- Gây hỏng bao bì, vật phẩm tiệt trùng nếu hấp thụ H₂O₂
- Là lỗi nghiêm trọng trong audit GMP, nếu không có quy trình giám sát tồn dư rõ ràng
3. Cách đo và giám sát nồng độ H₂O₂ sau khử khuẩn
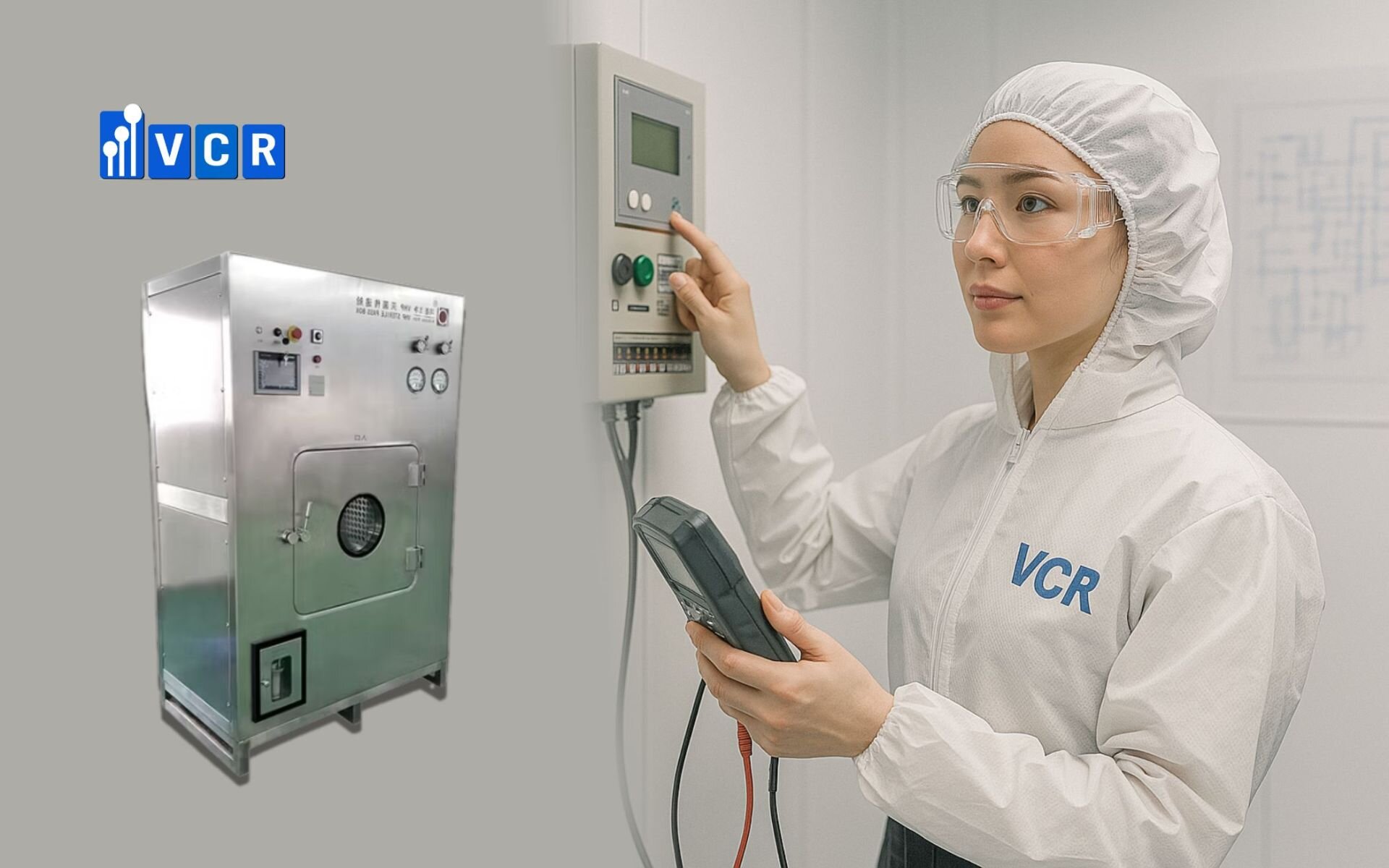
3.1. Các phương pháp đo nồng độ H₂O₂ phổ biến
- Gắn cố định bên trong buồng Pass Box hoặc đường ống xả khí
- Kết nối với bộ điều khiển trung tâm hoặc màn hình hiển thị ngoài
- Khi nồng độ xuống <1 ppm → cảm biến báo hiệu đèn xanh → cho phép mở cửa
2. Máy đo cầm tay (Portable H₂O₂ Detector)
- Sử dụng khi kiểm tra định kỳ hoặc backup cho cảm biến cố định
- Đưa đầu dò vào buồng Pass Box sau khử khuẩn để đo giá trị thực tế
- Hiển thị ppm trực tiếp, có thể lưu lại kết quả để phục vụ truy xuất GMP
3.2. Giám sát kết hợp hệ thống interlock Pass Box
- Nhiều model Pass Box cao cấp được tích hợp sẵn:
- Cảm biến H₂O₂
- Bộ điều khiển tự động hóa
- Liên động cửa thông minh: chỉ cho phép mở cửa sau khi đạt ngưỡng an toàn
- Tự động đếm ngược thời gian xả khí
- Hiển thị trạng thái nồng độ H₂O₂ (Đỏ – Vàng – Xanh)
- Ghi log thời điểm đạt ngưỡng <1 ppm → hỗ trợ truy xuất trong audit
3.3. Hiệu chuẩn và kiểm định cảm biến định kỳ
- Cảm biến H₂O₂ (dạng điện hóa hoặc PID) cần hiệu chuẩn định kỳ 6–12 tháng/lần
- Đảm bảo kết quả đo chính xác, tránh tình trạng báo sai (false-safe hoặc false-alarm)
- Có thể liên kết với đơn vị hiệu chuẩn đạt ISO 17025 để đảm bảo hồ sơ đầy đủ
4. Quy trình xả khí và đảm bảo an toàn sau chu trình VHP
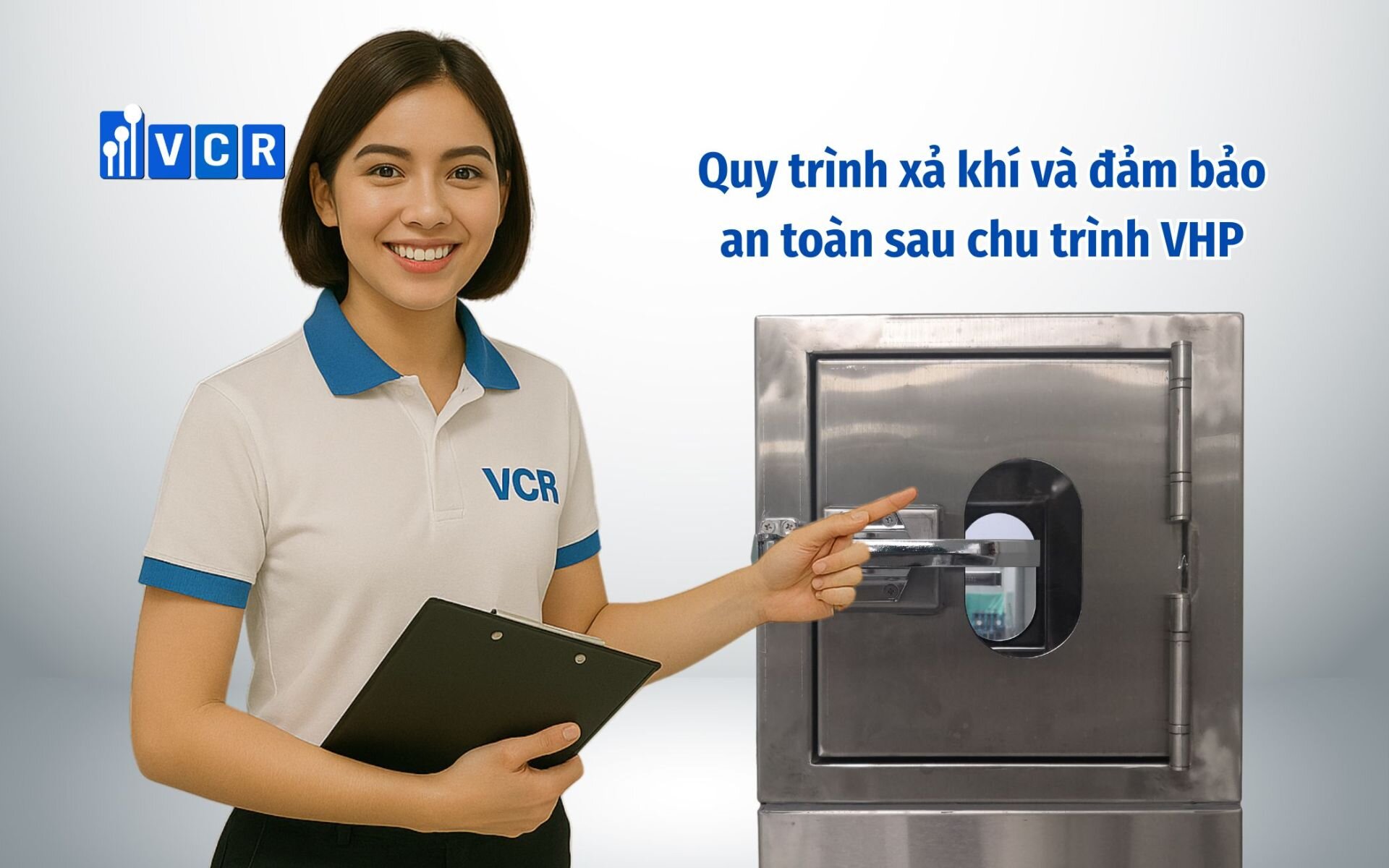
4.1. Giai đoạn Aeration – xả khí sau khử khuẩn
- Diễn ra sau khi kết thúc giai đoạn dwell (giữ hơi)
- Thời gian thường kéo dài 10–30 phút, tùy vào thể tích buồng, lưu lượng gió và hiệu suất hệ thống xả
- Mục tiêu: giảm nồng độ H₂O₂ từ mức khử khuẩn (200–1000 ppm) xuống dưới ngưỡng an toàn (<1 ppm)
4.2. Các phương pháp xả khí phổ biến
- Quạt hút trong Pass Box đẩy hơi H₂O₂ qua bộ lọc
- Mở đường xả khí về ống gió chung hoặc buồng hút trung tâm
- Yêu cầu có cảm biến đo nồng độ kiểm soát liên tục trong suốt quá trình
2. Xả cưỡng bức + lọc xúc tác
- Dùng quạt cưỡng bức + bộ xúc tác khử H₂O₂ thành nước và oxy
- Lọc xúc tác thường là màng bạc (Ag), MnO₂ hoặc màng carbon xúc tác
- Cho tốc độ khử nhanh, thường dùng trong dây chuyền vô trùng, isolator
4.3. Kiểm soát liên động an toàn
- Cửa Pass Box phải bị khóa liên động cho đến khi H₂O₂ < 1 ppm
- Có thể lập trình tín hiệu mở cửa khi:
- Cảm biến báo < 1 ppm
- Đèn cảnh báo chuyển từ đỏ/vàng sang xanh
- Chu trình aeration hoàn tất và ghi log tự động
4.4. Một số lưu ý quan trọng khi xả khí
- Tuyệt đối không mở cửa cưỡng bức khi chưa đạt mức an toàn
- Không đứng gần cửa xả hoặc đường thoát khí khi hệ thống đang aeration
- Luôn kiểm tra độ kín gioăng cửa – tránh rò rỉ H₂O₂ ra môi trường phòng sạch
- SOP cần quy định rõ:
- Thời gian tối thiểu xả khí
- Cách ghi nhận nồng độ
- Phản ứng khi phát hiện vượt ngưỡng
5. Rủi ro nếu nồng độ H₂O₂ vượt ngưỡng cho phép
5.1. Ảnh hưởng đến sức khỏe người vận hành
- Kích ứng đường hô hấp: ho khan, rát họng, tức ngực khi hít phải H₂O₂ nồng độ >1 ppm
- Kích ứng mắt và da: cay mắt, đỏ mắt, nóng rát da nếu tiếp xúc trực tiếp
- Nguy cơ nhiễm độc nhẹ nếu tiếp xúc lặp lại nhiều lần, đặc biệt trong phòng kín
5.2. Ăn mòn vật liệu thiết bị – giảm tuổi thọ Pass Box
- H₂O₂ dư tồn tại lâu trong buồng sẽ gây oxy hóa inox, bạc màu bề mặt, phồng gioăng
- Làm hỏng bộ lọc HEPA/ULPA nếu tiếp xúc nhiều lần mà không được xả sạch
- Có thể làm mất tính chất vật lý của vật phẩm nhựa, cao su, bao bì sơ cấp
5.3. Gây ảnh hưởng đến sản phẩm hoặc mẫu kiểm nghiệm
- Nếu mẫu vật (lọ tiêm, bao bì, vật tư vô trùng) tiếp xúc với H₂O₂ tồn dư:
- Có thể bị hấp thụ hơi hóa chất → ảnh hưởng chất lượng hoặc tương tác dược lý
- Mất tính vô trùng nếu bề mặt bị ẩm do ngưng tụ
- Mẫu kiểm nghiệm vi sinh bị sai lệch kết quả
5.4. Vi phạm tiêu chuẩn GMP và dễ bị lỗi trong audit
- Không kiểm soát nồng độ H₂O₂ sau chu trình là lỗi nặng trong kiểm tra:
- EU-GMP Annex 1: yêu cầu truy xuất rõ ràng chu trình khử khuẩn và an toàn vận hành
- WHO GMP: đề cập rõ trách nhiệm đảm bảo an toàn hóa chất trong phòng sạch
- Dễ bị auditor đặt câu hỏi:
- Có cảm biến kiểm soát không?
- Có log nồng độ sau khử khuẩn không?
- Có cảnh báo khi vượt ngưỡng?
- Có SOP xử lý sự cố khí độc còn dư?
6. Khuyến nghị vận hành và thiết kế Pass Box khử khuẩn VHP an toàn
6.1. Thiết kế Pass Box VHP tích hợp đầy đủ tính năng an toàn
- Tích hợp cảm biến đo H₂O₂ (electrochemical sensor hoặc PID) để giám sát nồng độ dư trong buồng
- Bộ điều khiển tự động hiển thị trạng thái chu trình, cảnh báo mức an toàn
- Liên động cửa thông minh: chỉ mở khi nồng độ < 1 ppm hoặc theo cài đặt
- Đèn cảnh báo 3 màu (Đỏ – Vàng – Xanh) gắn ngoài giúp nhận diện trạng thái từ xa
- Quạt xả tốc độ cao + bộ lọc xúc tác hỗ trợ giai đoạn aeration nhanh và sạch
6.2. SOP vận hành rõ ràng, chi tiết
- SOP phải quy định rõ từng bước:
- Chu trình khử khuẩn
- Cách kiểm tra nồng độ tồn dư
- Điều kiện cho phép mở cửa
- Quy trình xử lý khi vượt ngưỡng an toàn
- Có log ghi nhận tự động hoặc bán tự động để phục vụ audit
6.3. Đào tạo nhân sự vận hành định kỳ
- Cập nhật kiến thức về tác động của H₂O₂ lên sức khỏe và vật liệu
- Kỹ năng đọc cảm biến, xử lý tình huống khẩn cấp khi có rò rỉ khí
- Quy trình đóng – mở cửa Pass Box đúng thời điểm, tránh cưỡng bức
6.4. Hiệu chuẩn định kỳ cảm biến và thiết bị đo nồng độ
- Cảm biến H₂O₂ cần được hiệu chuẩn mỗi 6–12 tháng, tùy theo tần suất sử dụng
- Thiết bị đo cầm tay nên được kiểm định định kỳ để đảm bảo độ chính xác
- Toàn bộ hồ sơ hiệu chuẩn nên lưu trữ trong bộ hồ sơ thiết bị GMP
- Bản vẽ kỹ thuật, sơ đồ cảm biến
- Log chu trình mẫu
- Chứng chỉ hiệu chuẩn cảm biến
- Hướng dẫn bảo trì quạt xả và lọc xúc tác
7. Kết luận – Nồng độ H₂O₂ thấp hơn 1 ppm là ngưỡng an toàn bắt buộc
- 1 ppm không chỉ là một con số – đó là ranh giới đỏ giữa an toàn và rủi ro.
- Đảm bảo đủ cảm biến – xả khí đúng quy trình – ghi nhận đầy đủ thông số là điều kiện tối thiểu.
- Càng nhiều thiết bị tích hợp tự động, càng dễ vận hành và chứng minh sự tuân thủ trước các đoàn kiểm tra.
- Hotline/Zalo 24/7: 090.123.9008
- Website: https://vietnamcleanroom.com
- Email: [email protected]