Customized passboxes are essential for specialized food manufacturing processes, ensuring contamination control and compliance with industry standards. Discover how tailored passbox solutions can optimize your workflow, enhance product safety, and meet the unique requirements of your cleanroom environment.
Summaries
- I. Introduction passbox
- II. Specialized Food Manufacturing Processes Requiring Custom Passbox
- III. Design Considerations for Customized Passbox
- IV. Regulatory Compliance and Standards
- D. Impact of Non-Compliance
- V. Implementation Strategies for Customized Passbox
- VI. Maintenance and Validation of Customized Passbox
Join vcr clean room equipment to learn more about customized Passboxes for specialized food production processes through the article below.
I. Introduction passbox
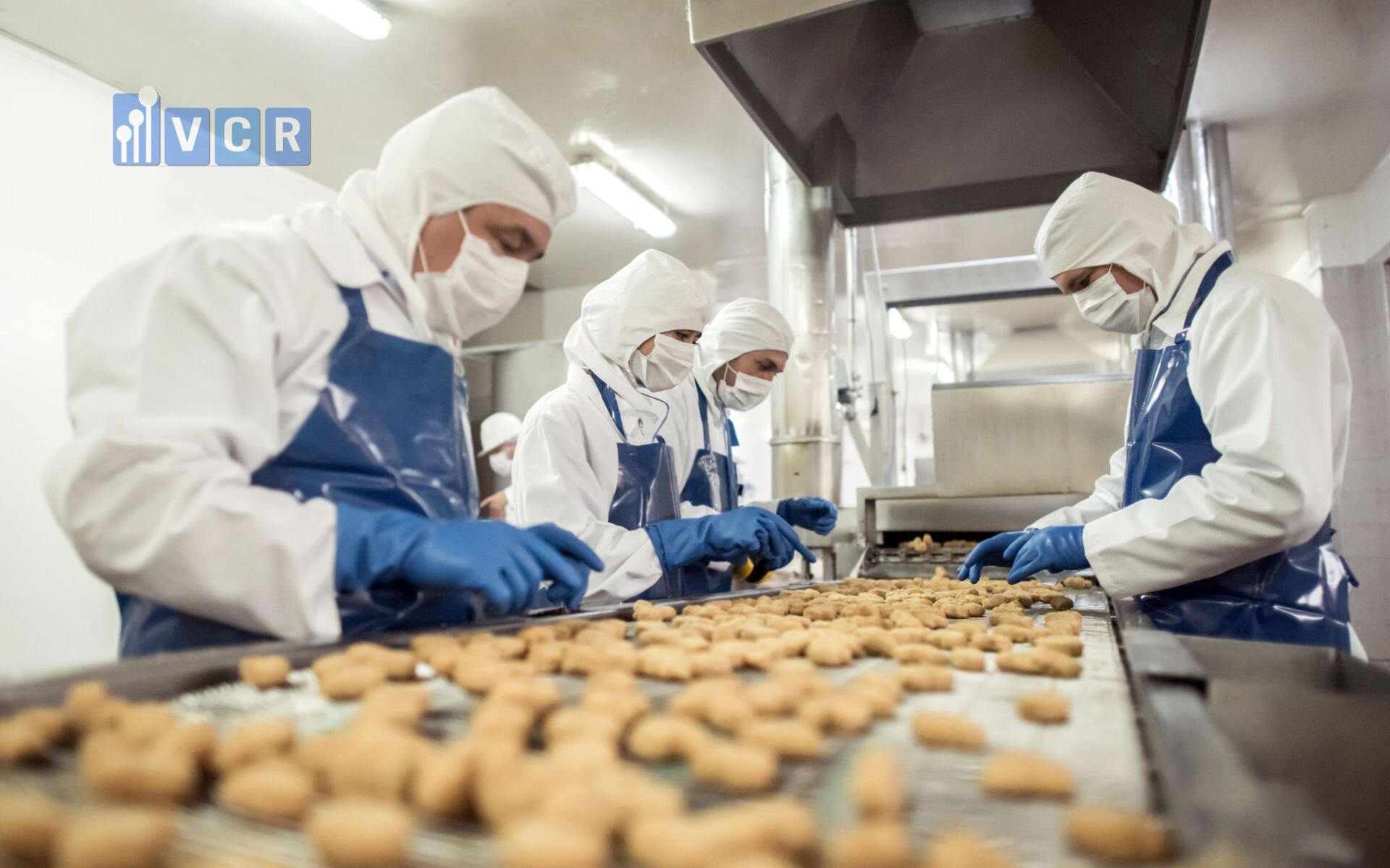
In the dynamic landscape of food manufacturing, maintaining stringent hygiene standards and operational efficiency is paramount. The passbox has emerged as an essential component within food factories, serving as a controlled gateway for the transfer of materials between different processing areas. This enclosed unit facilitates the seamless movement of raw ingredients, packaging materials, and finished products while minimizing the risk of contamination. By ensuring that materials are transferred in a controlled manner, the passbox plays a critical role in upholding the cleanliness and efficiency that are vital for producing safe and high-quality food products.
The design of the passbox has significantly evolved over the years. Historically, standard passbox were simple airlock systems designed to prevent the ingress of contaminants during material transfers. However, as the food industry has advanced, so too have the requirements for contamination control and operational flexibility. This evolution has driven the transition from one-size-fits-all solutions to customized passbox tailored to meet the specific needs of specialized food manufacturing processes. Customized designs now incorporate advanced features such as automated door controls, integrated sanitization systems, and enhanced airflow management to address unique challenges in various food production environments.
Customization is increasingly important in specialized food manufacturing due to the diverse and demanding requirements of different processes. High-hygiene standards are essential in areas handling ready-to-eat meals, allergen-controlled facilities must prevent cross-contamination, and operations dealing with potent ingredients require robust containment measures. Customized passbox offer numerous benefits, including enhanced contamination control, improved workflow efficiency, and compliance with specific industry standards. These tailored solutions ensure that each food manufacturing process operates smoothly and safely, meeting both regulatory requirements and consumer expectations.
This article is designed for food manufacturing engineers, quality assurance professionals, facility designers, and regulatory compliance officers. It aims to provide in-depth insights into the customization of passbox for specialized food manufacturing needs. By exploring design considerations, regulatory compliance, implementation strategies, and real-world applications, this article offers a comprehensive guide to optimizing passbox systems. The subsequent sections will delve into the specific processes that benefit from customized passbox, the critical design elements involved, and the best practices for ensuring these systems enhance both safety and efficiency in food production environments.
II. Specialized Food Manufacturing Processes Requiring Custom Passbox
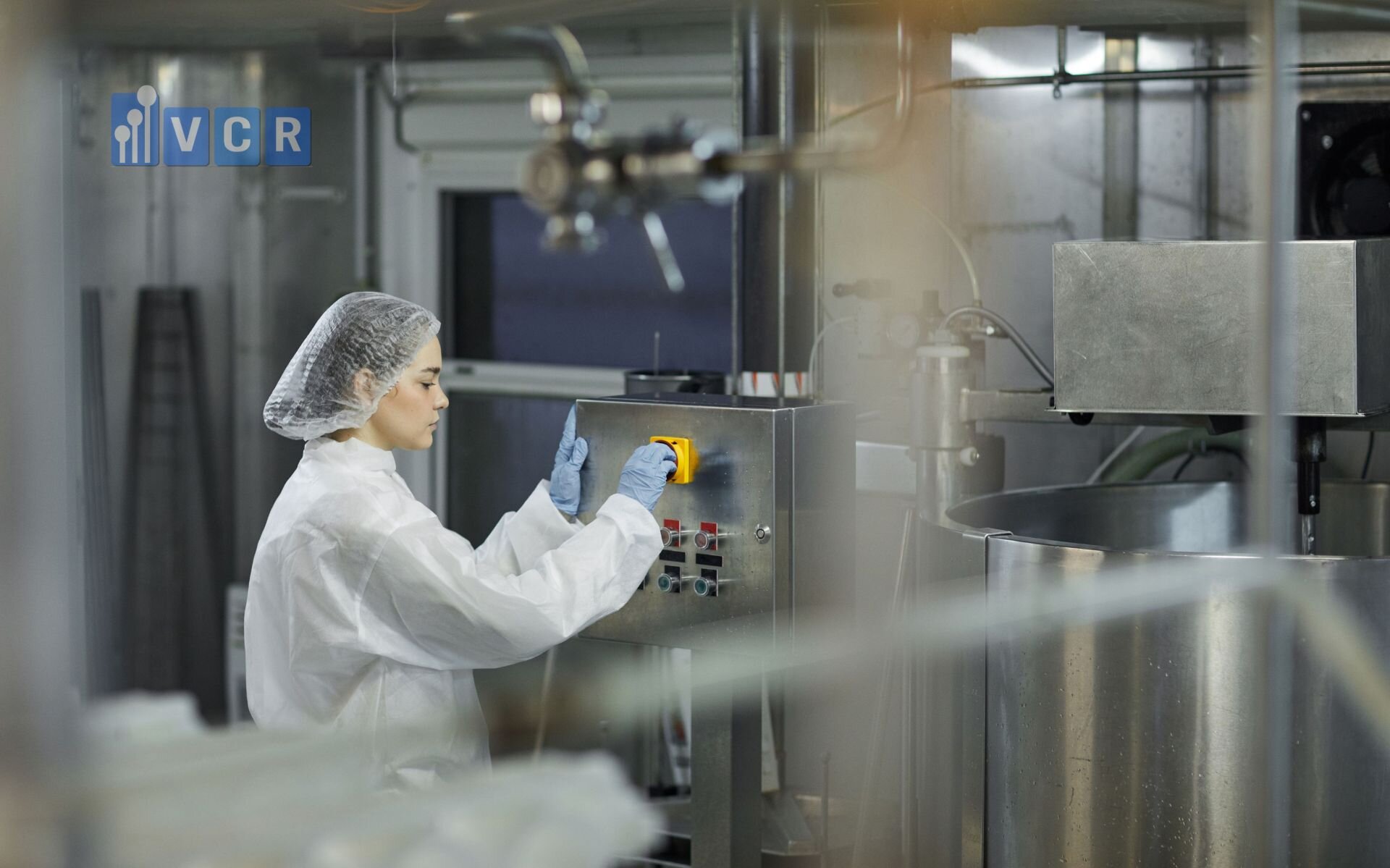
In the realm of cleanroom food manufacturing, the precision and reliability of material transfer systems are crucial for maintaining product integrity and ensuring food safety. Customized passbox are tailored to address the unique challenges posed by various specialized food manufacturing processes. This section explores the specific environments and requirements that necessitate bespoke passbox solutions, highlighting the customization strategies that enhance contamination control, operational efficiency, and regulatory compliance.
A. High-Humidity and Moisture-Rich Environments
1. Challenges in High-Humidity Areas
Food manufacturing facilities often operate in environments with high humidity levels, particularly in areas involved in processing moisture-rich products like baked goods, confectioneries, and ready-to-eat meals. High humidity poses several challenges:
Corrosion: Elevated moisture levels accelerate the corrosion of metal components within passbox, compromising their structural integrity and functionality.
Mold Growth: Persistent moisture fosters the growth of mold and mildew on surfaces, which can contaminate food products and create health hazards.
Equipment Malfunction: Excessive humidity can lead to electrical failures and mechanical issues in passbox components, disrupting material transfer processes and increasing maintenance costs.
2. Customization Solutions
To mitigate these challenges, customized passbox incorporate specific design features:
Materials Resistant to Moisture: Utilizing stainless steel alloys such as 316L, which offer superior corrosion resistance, ensures durability in high-humidity settings. Additionally, high-grade plastics with moisture-resistant properties can be employed for components prone to exposure.
Enhanced Sealing Mechanisms: Implementing advanced sealing technologies, such as gasketed doors and airtight connections, prevents moisture ingress and maintains internal environmental conditions. Automated door seals that engage upon closure further enhance the passbox’s ability to resist moisture penetration.
Integrated Dehumidification Systems: Incorporating built-in dehumidifiers or moisture-absorbing materials within passbox helps regulate internal humidity levels, reducing the risk of mold growth and corrosion.
B. Allergen-Controlled Manufacturing
1. Importance of Allergen Management
In food manufacturing, managing allergens is critical to prevent cross-contamination and ensure compliance with stringent labeling laws. Cross-contamination can have severe health implications for consumers with food allergies and can result in costly recalls and reputational damage for manufacturers.
2. Customized Features
Customized passbox designed for allergen-controlled environments include:
Dedicated Passbox for Allergen-Free Zones: Establishing separate passbox for allergen-free and allergen-containing areas minimizes the risk of cross-contamination. These passbox are isolated to ensure that allergenic substances do not migrate between zones.
Easy-to-Clean Surfaces: Surfaces within the passbox are finished with smooth, non-porous materials that resist allergen adhesion and facilitate thorough cleaning. Automated cleaning systems, such as CIP (Clean-In-Place) technologies, can be integrated to ensure consistent sanitation.
Specialized Airflow Systems: Implementing HEPA-filtered airflow ensures that airborne allergens are effectively captured and removed. Positive pressure within allergen-free passbox prevents the ingress of allergenic particles from adjacent areas.
C. Handling of Potent or Hazardous Ingredients
1. Safety and Contamination Risks
Handling potent or hazardous ingredients, such as concentrated flavorings, preservatives, or chemical additives, presents significant safety and contamination risks. These substances can pose health hazards to workers and contaminate food products if not managed properly.
2. Design Modifications
Customized passbox for handling hazardous ingredients incorporate several safety-focused design modifications:
Containment Features: Secondary barriers, such as double-door systems or spill containment trays, prevent the escape of hazardous substances during material transfers. These features ensure that any accidental spills or leaks are contained within the passbox, protecting both personnel and products.
Specialized Ventilation: Enhanced ventilation systems, including dedicated exhaust fans and chemical-resistant ductwork, remove airborne contaminants and maintain a safe working environment. Integration with facility-wide ventilation ensures that hazardous fumes are effectively diluted and expelled.
Automated Safety Controls: Incorporating sensors and automated shut-off mechanisms detects the presence of hazardous substances and triggers containment protocols. These controls enhance safety by minimizing the need for manual intervention in potentially dangerous situations.
D. Sterile or Aseptic Processing
1. Maintaining Sterility
In sterile or aseptic food processing, such as the production of ready-to-eat meals and beverages, maintaining an uncontaminated environment is crucial. Even minor breaches in sterility can lead to product spoilage and health risks.
2. Customized Solutions
Customized passbox for sterile processing include:
HEPA-Filtered Airflow: High-efficiency particulate air (HEPA) filters ensure that incoming and outgoing air is free from contaminants. This filtration is essential for maintaining sterile conditions within the passbox and preventing microbial ingress.
Automated Door Controls: Automated mechanisms control the opening and closing of passbox doors, reducing the risk of human error and maintaining continuous sterile conditions. Features such as timed door closures and interlock systems ensure that both doors are not open simultaneously.
Integrated Sanitization Systems: Incorporating sanitization technologies, such as UV-C light systems or vaporized hydrogen peroxide (VHP) dispensers, ensures that passbox are regularly decontaminated. These systems eliminate residual microorganisms and maintain aseptic conditions between material transfers.
E. Temperature-Controlled Manufacturing
1. Challenges with Temperature Variations
Temperature-controlled manufacturing processes, such as those involving refrigeration or freezing, present unique challenges:
Thermal Expansion: Repeated temperature fluctuations can cause materials within the passbox to expand and contract, leading to wear and potential breaches in seals.
Condensation: Temperature differences between adjoining areas can result in condensation within the passbox, fostering microbial growth and corrosion.
2. Customization Strategies
To address these challenges, customized passbox incorporate:
Insulated Passbox: Insulation materials help maintain consistent internal temperatures, reducing thermal expansion and minimizing condensation. Double-walled constructions and thermal barriers prevent external temperature fluctuations from affecting the passbox environment.
Temperature-Resistant Materials: Utilizing materials that withstand extreme temperatures ensures durability and integrity. For instance, using stainless steel or specialized plastics that do not degrade under cold conditions preserves the passbox’s functionality.
Integration with HVAC Systems: Coordinating passbox design with the facility’s HVAC systems ensures that temperature and humidity levels are consistently controlled. Automated temperature and humidity sensors adjust airflow and cooling parameters to maintain optimal conditions within the passbox.
III. Design Considerations for Customized Passbox
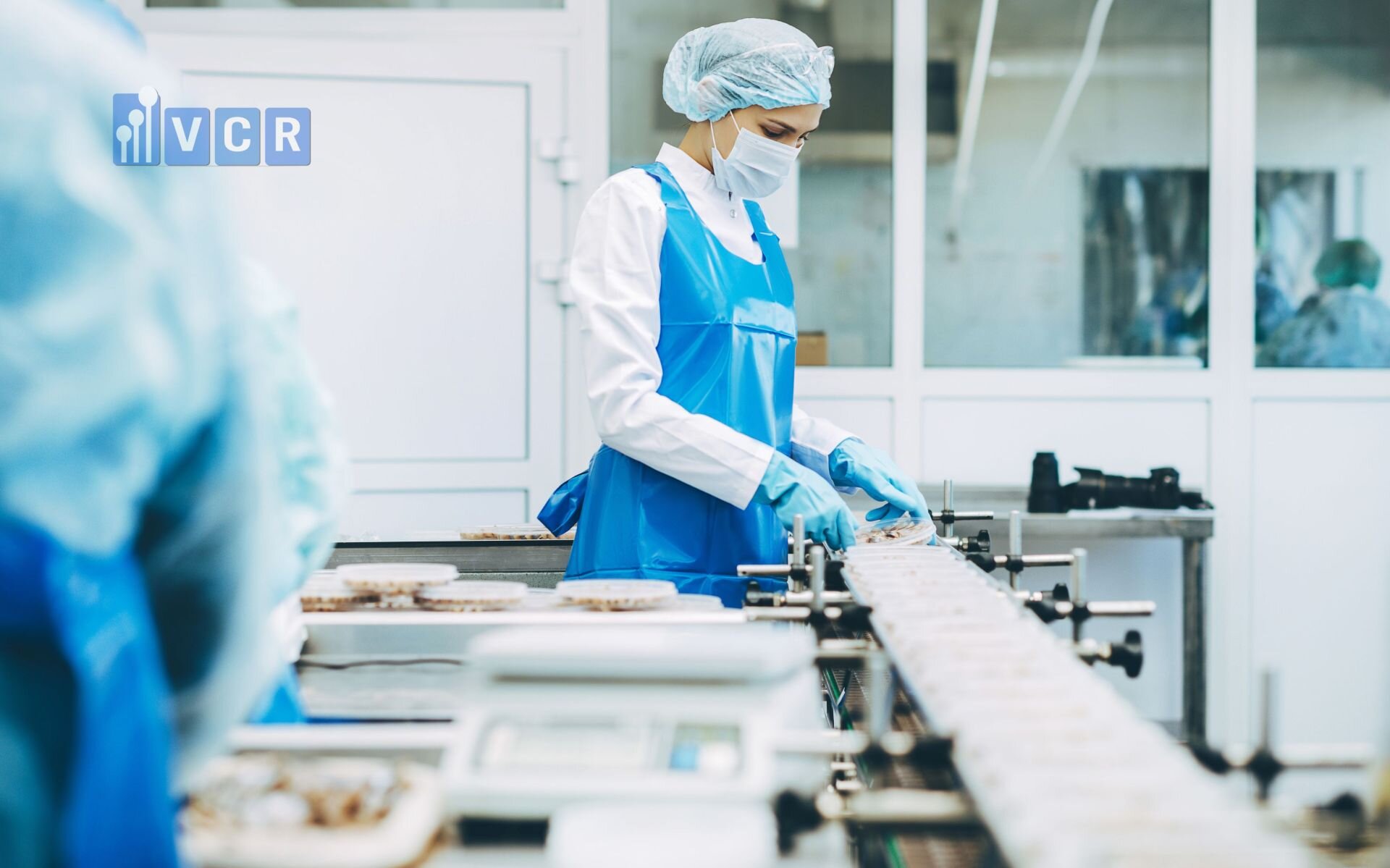
Designing a customized passbox for specialized food manufacturing processes requires a meticulous approach that addresses the unique challenges and requirements of different production environments. Key design considerations encompass material selection, airflow and ventilation systems, structural design and ergonomics, sealing and containment features, and technological integrations. Each of these elements plays a vital role in ensuring that the passbox not only meets hygiene and safety standards but also enhances operational efficiency and compliance within specialized food manufacturing settings.
A. Material Selection
1. Hygienic and Durable Materials
The selection of materials for passboxes is critical in maintaining hygiene and durability, especially in food manufacturing environments where contamination risks are high.
Stainless Steel: Renowned for its excellent corrosion resistance, stainless steel (particularly grades like 304 and 316L) is a preferred material in passbox construction. It offers a smooth, non-porous surface that is easy to clean and sanitize, minimizing microbial harboring and facilitating compliance with stringent hygiene standards.
High-Grade Plastics: In areas where metal components may pose handling difficulties or where additional insulation is required, high-grade plastics such as polycarbonate or polypropylene are utilized. These materials provide durability, chemical resistance, and ease of maintenance, ensuring that passboxes remain robust under various operational conditions.
2. Resistance to Environmental Factors
Customized passboxes must withstand the specific environmental challenges of their intended use areas.
Corrosion-Resistant Coatings: To further enhance the longevity of stainless steel passboxes in high-humidity or moisture-rich environments, corrosion-resistant coatings such as epoxy or polyurethane are applied. These coatings protect against moisture ingress and chemical exposure, preventing rust and degradation over time.
UV-Resistant Materials: In facilities where passboxes are exposed to ultraviolet (UV) light, either from external sources or integrated UV sanitization systems, UV-resistant materials are essential. These materials prevent degradation, discoloration, and loss of structural integrity, ensuring that passboxes maintain their functionality and appearance.
B. Airflow and Ventilation Systems
1. Tailored Airflow Patterns
Effective contamination control within passboxes relies heavily on the design of airflow patterns, which must be tailored to the specific needs of the manufacturing process.
Laminar Flow: In sterile or aseptic processing environments, laminar airflow is essential for maintaining sterility. Laminar flow systems provide a unidirectional, consistent air movement that sweeps contaminants away from critical areas, reducing the risk of microbial contamination during material transfers.
Turbulent Flow: For less critical areas or processes where high levels of particulate control are not as stringent, turbulent airflow can be employed. Turbulent systems promote better mixing of air, which can be beneficial in environments requiring uniform temperature and humidity levels but are less dependent on absolute sterility.
2. Integrated Ventilation Controls
Advanced ventilation controls are integral to maintaining optimal environmental conditions within customized passboxes.
Automated Airflow Adjustments: Automation systems adjust airflow rates based on real-time monitoring data, ensuring that the passbox maintains the desired pressure differentials and airflow patterns regardless of external changes or operational demands. This adaptability enhances contamination control and ensures consistent performance.
HEPA Filtration Integration: High-Efficiency Particulate Air (HEPA) filters are incorporated into the ventilation systems of passboxes to capture airborne particulates and microbial contaminants. HEPA filters are crucial in sterile and allergen-controlled environments, providing a high level of filtration that upholds strict hygiene standards.
C. Structural Design and Ergonomics
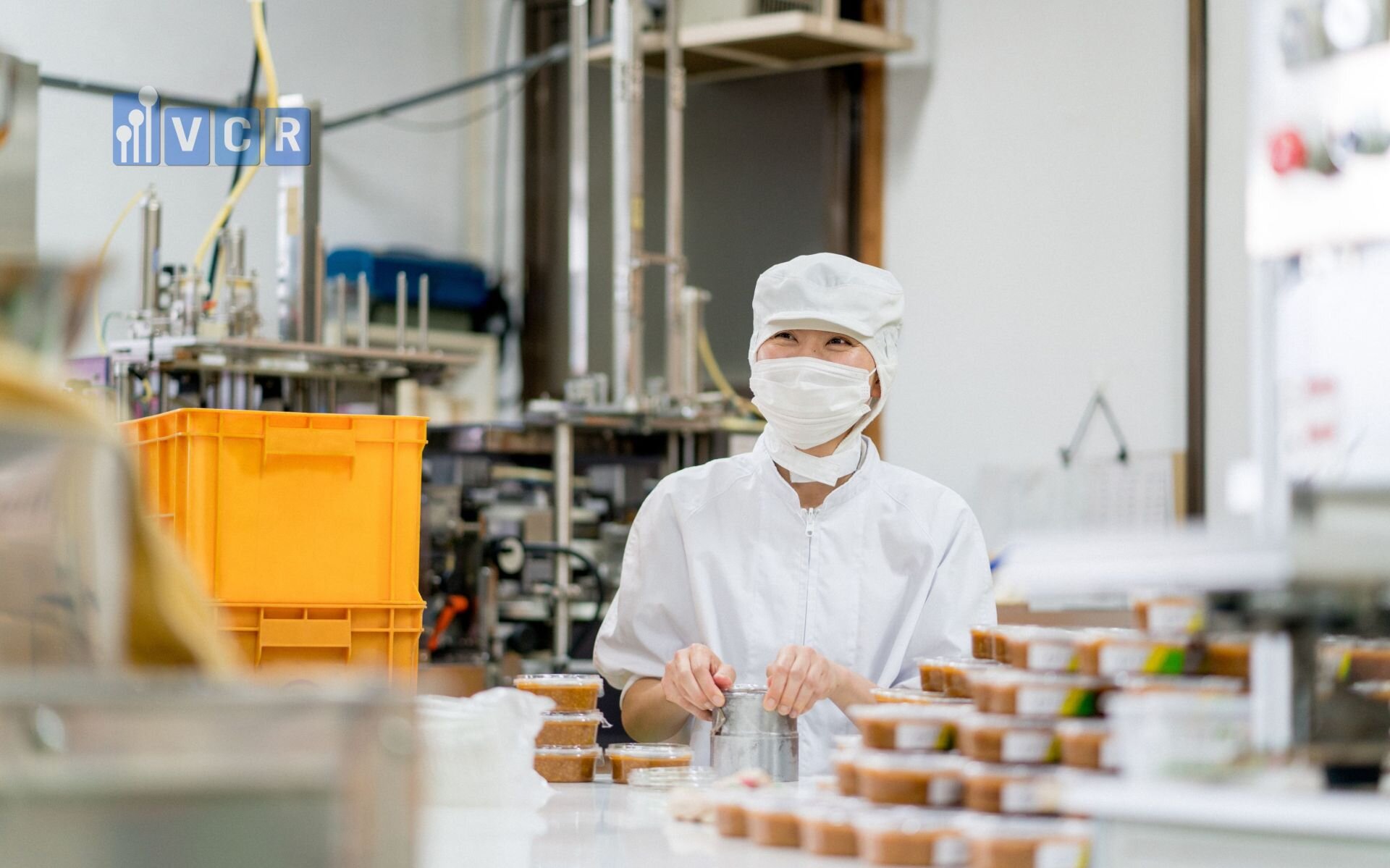
1. Space Optimization
Efficient use of space is a key consideration in the structural design of customized passboxes, particularly in facilities where floor space is limited.
Fit Within Existing Factory Layouts: Customized passboxes are designed to seamlessly integrate into existing factory layouts without disrupting workflow. Modular designs allow for flexibility in installation, accommodating various wall thicknesses and spatial configurations.
Modular Designs: Modular passboxes can be easily reconfigured or expanded to meet evolving production needs. This adaptability is particularly beneficial in dynamic manufacturing environments where production lines may be frequently updated or scaled.
2. User-Friendly Interfaces
The usability of passboxes significantly impacts operational efficiency and worker safety.
Ergonomic Door Handles: Passboxes are equipped with ergonomic door handles that facilitate easy opening and closing, reducing strain on workers and minimizing the risk of accidental drops or spills during material transfers.
Easy Access Points for Materials: Design features such as wide access ports, smooth internal surfaces, and strategically placed openings ensure that materials can be transferred swiftly and safely. This minimizes handling time and reduces the potential for contamination during transfers.
D. Sealing and Containment Features
1. Enhanced Sealing Mechanisms
Effective sealing is paramount in preventing contamination and maintaining controlled environmental conditions within passboxes.
Automatic Door Seals: Automated sealing mechanisms engage upon door closure, ensuring an airtight connection that maintains pressure differentials and prevents ingress of contaminants. These systems reduce the reliance on manual sealing, enhancing consistency and reliability.
Airtight Connections: Passboxes feature airtight connections between doors and the main structure, utilizing gaskets and sealing strips made from materials that maintain integrity under varying environmental conditions. This ensures that passboxes remain effective barriers against contaminants.
2. Secondary Containment Options
Additional containment features provide an extra layer of protection against accidental spills or leaks.
Double-Door Systems: Double-door configurations create an intermediate space that acts as a buffer zone, preventing direct exposure of critical environments to potential contaminants. This setup is particularly useful in allergen-controlled and sterile manufacturing processes.
Spill Containment Trays: Integrated spill trays capture any accidental leaks or spills, containing hazardous substances within the passbox and preventing them from spreading to the surrounding environment. This feature is essential in facilities handling potent or hazardous ingredients.
E. Technological Integrations
1. Automation and Smart Technologies
Incorporating automation and smart technologies into passbox systems enhances operational efficiency and contamination control.
Automated Material Transfer: Automated systems facilitate the seamless transfer of materials between different areas without manual intervention. This reduces human error, minimizes contamination risks, and speeds up production processes.
RFID Tracking: Radio-Frequency Identification (RFID) technology enables real-time tracking of materials as they pass through the passbox. This integration enhances traceability, ensuring that all materials are accounted for and comply with quality standards.
2. Real-Time Monitoring Systems
Advanced monitoring systems provide continuous oversight of critical environmental parameters within passboxes.
Sensors for Pressure, Humidity, Particle Counts: Integrated sensors continuously monitor key parameters such as pressure differentials, humidity levels, and particulate concentrations. Real-time data collection ensures that any deviations from set standards are promptly detected and addressed.
Integration with SCADA Systems: Supervisory Control and Data Acquisition (SCADA) systems integrate passbox monitoring data into the facility’s central control system. This integration allows for centralized oversight, automated alerts, and data analytics that support proactive maintenance and operational decision-making.
IV. Regulatory Compliance and Standards
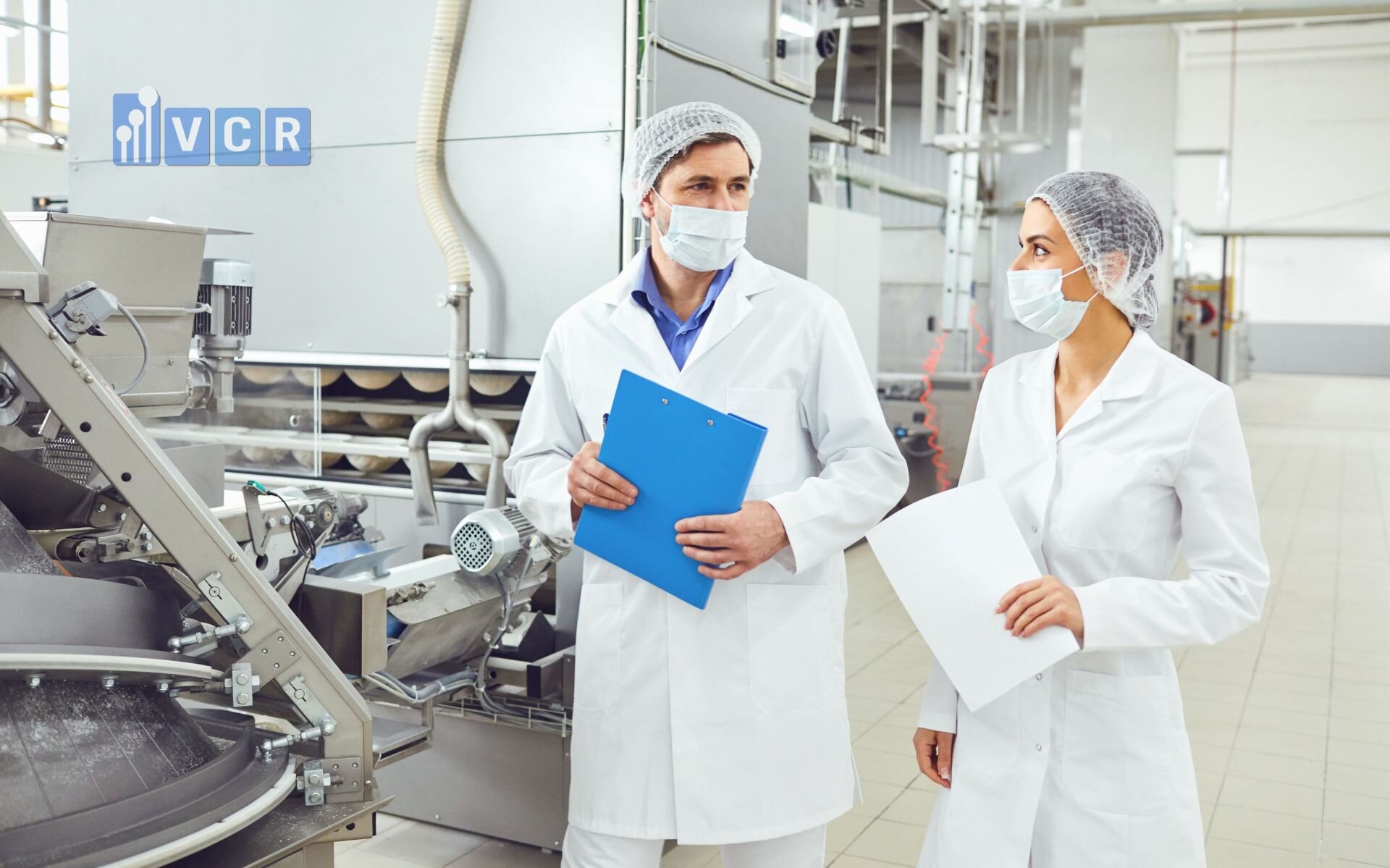
Ensuring regulatory compliance is paramount in the design and operation of customized passboxes within specialized food manufacturing processes. Adhering to stringent food safety regulations and international standards not only safeguards consumer health but also fortifies the manufacturer’s reputation and operational integrity. This section delves into the relevant food safety regulations, international standards and certifications, documentation and validation requirements, and the profound impacts of non-compliance on food manufacturing entities.
A. Relevant Food Safety Regulations
1. FDA Food Safety Modernization Act (FSMA)
The Food Safety Modernization Act (FSMA), enacted by the U.S. Food and Drug Administration (FDA), represents a significant overhaul of food safety regulations, shifting the focus from reactive measures to proactive prevention. FSMA imposes comprehensive requirements that directly affect the design and operation of passboxes in food manufacturing facilities.
Preventive Controls: FSMA mandates the implementation of preventive controls for human and animal food. This includes identifying potential hazards, implementing measures to prevent contamination, and continuously monitoring these controls. Customized passboxes must be designed to meet these preventive measures by ensuring controlled material transfers that minimize contamination risks.
Sanitation Standards: FSMA emphasizes stringent sanitation standards. Passboxes must incorporate materials and design features that facilitate thorough cleaning and sanitization, preventing microbial growth and contamination.
Process Control and Monitoring: Continuous process control and monitoring are essential under FSMA. Customized passboxes should integrate real-time monitoring systems to track critical parameters such as airflow, humidity, and pressure differentials, ensuring compliance with FSMA’s proactive safety requirements.
Supplier Verification: FSMA requires verification of supplier compliance with food safety standards. Passboxes play a role in maintaining the integrity of materials transferred from suppliers, ensuring that incoming ingredients meet safety and quality standards before entering the production environment.
2. Hazard Analysis and Critical Control Points (HACCP)
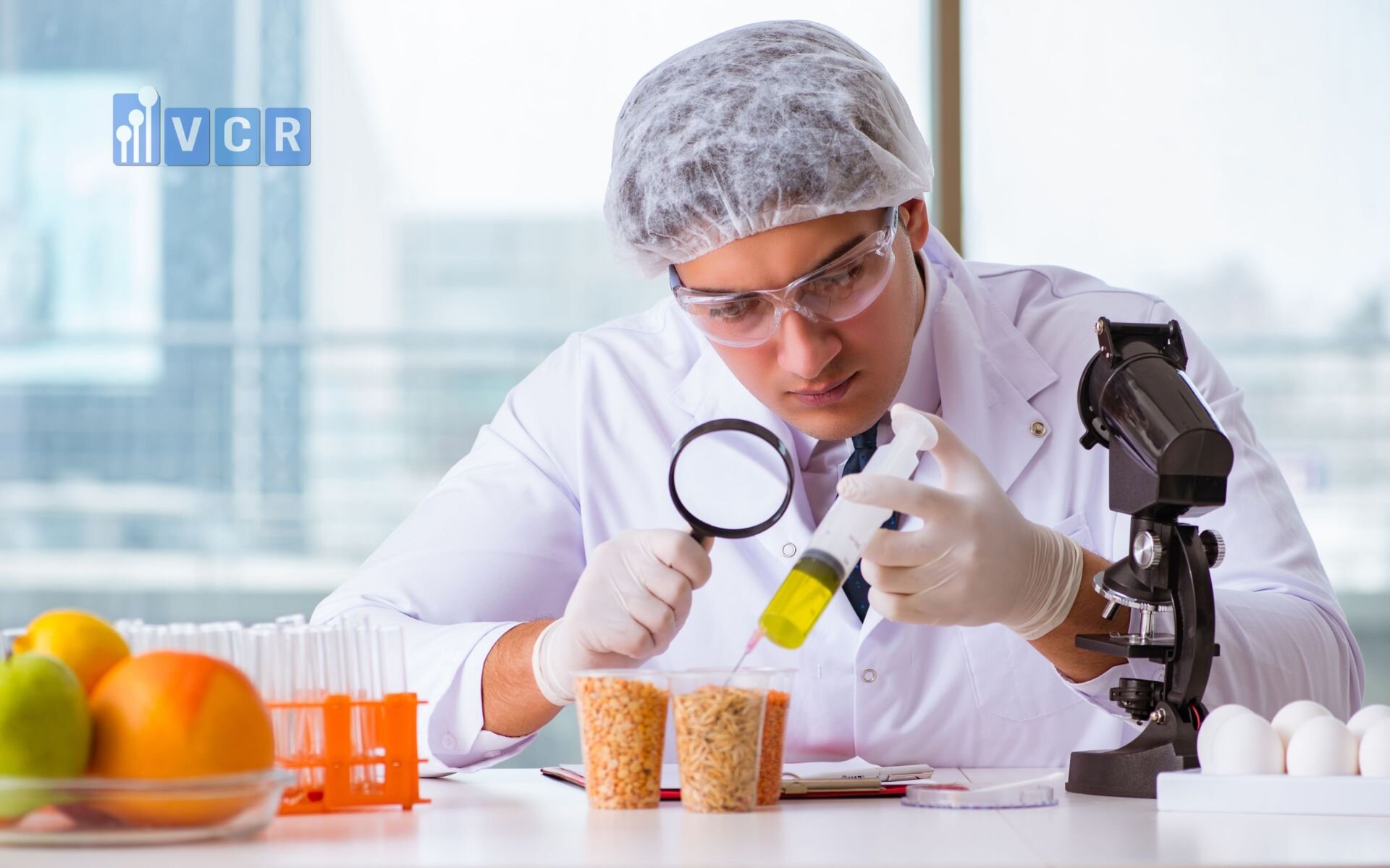
Hazard Analysis and Critical Control Points (HACCP) is a systematic preventive approach to food safety that identifies physical, chemical, and biological hazards in production processes and implements measures to reduce these risks to safe levels.
Integration of Passboxes into HACCP Plans: Passboxes must be seamlessly integrated into HACCP plans as critical control points (CCPs) where potential hazards can be controlled. For instance, the controlled transfer of materials through passboxes can prevent cross-contamination, especially in processes handling allergens or potent ingredients.
Critical Limits and Monitoring: Establishing critical limits for passbox operation, such as specific airflow rates and pressure differentials, is essential. Continuous monitoring of these limits ensures that passboxes function within safe parameters, thereby maintaining the overall safety and quality of the food products.
Corrective Actions: In the event of deviations from critical limits, corrective actions must be predefined and implemented. For example, if a passbox fails to maintain the required pressure differential, immediate actions such as recalibrating sensors or repairing seals must be undertaken to mitigate contamination risks.
B. International Standards and Certifications
1. ISO 22000: Food Safety Management
ISO 22000 is an internationally recognized standard for food safety management systems. It outlines the requirements for establishing, implementing, maintaining, and continually improving a food safety management system.
Compliance Considerations for Passboxes: To comply with ISO 22000, passboxes must be designed and operated to effectively control hazards identified in the food production process. This includes ensuring that passboxes are properly sanitized, maintained, and monitored to prevent contamination.
Systematic Approach: ISO 22000 promotes a systematic approach to food safety, emphasizing the importance of integrating passboxes into the broader food safety management system. This involves documenting passbox operations, maintaining traceability, and ensuring that passboxes contribute to the overall hazard control strategy.
Continuous Improvement: The standard encourages continuous improvement. Manufacturers must regularly review and update passbox designs and operational protocols based on performance data, audit findings, and technological advancements to enhance food safety outcomes.
2. Global Food Safety Initiative (GFSI) Standards
The Global Food Safety Initiative (GFSI) benchmarks global food safety standards, recognizing those that meet its stringent criteria. Compliance with GFSI standards is often a prerequisite for accessing international markets.
Alignment with Recognized Benchmarks: Customized passboxes must align with GFSI-recognized standards such as SQF (Safe Quality Food), BRC (British Retail Consortium), or FSSC 22000. This alignment ensures that passboxes meet the high food safety and quality requirements demanded by global retailers and consumers.
Third-Party Certifications: Achieving third-party certifications under GFSI standards provides external validation of passbox compliance and effectiveness. These certifications enhance the credibility of food manufacturers and facilitate market access by meeting international safety benchmarks.
Best Practices Integration: GFSI standards promote the adoption of best practices in food safety management. Customized passboxes should incorporate these best practices, such as robust sanitization protocols, advanced monitoring systems, and ergonomic designs, to ensure optimal performance and compliance.
C. Documentation and Validation Requirements
1. Validation Protocols for Customized Passbox
Comprehensive validation protocols are essential to demonstrate that customized passboxes meet all design and operational specifications.
Installation Qualification (IQ): Verifies that the passbox is installed correctly according to design specifications. This includes checking materials, installation procedures, and environmental conditions.
Operational Qualification (OQ): Assesses whether the passbox operates within defined parameters under normal and stress conditions. This involves testing airflow rates, pressure differentials, and automation systems to ensure they function as intended.
Performance Qualification (PQ): Confirms that the passbox consistently performs effectively under real-world conditions over an extended period. PQ involves monitoring the passbox during actual production processes to validate its ongoing reliability and effectiveness in contamination control.
2. Record-Keeping and Traceability
Maintaining detailed records is crucial for demonstrating compliance during audits and inspections.
Comprehensive Records: Detailed documentation of all validation activities, maintenance logs, calibration records, and monitoring data must be maintained. These records provide evidence that passboxes are functioning correctly and are being managed in accordance with regulatory requirements.
Traceability: Ensuring traceability of materials and processes through passboxes is vital for identifying the source of any contamination incidents. This involves recording the movement of materials through passboxes, linking passbox operations to specific production batches, and maintaining logs of environmental parameters.
Audit Readiness: Organized and accessible records facilitate audit readiness, allowing manufacturers to quickly provide necessary documentation during regulatory inspections. This ensures that compliance can be demonstrated efficiently and effectively, minimizing the risk of penalties or operational disruptions.
D. Impact of Non-Compliance
1. Regulatory Penalties
Failure to comply with food safety regulations and standards can result in severe consequences for food manufacturers.
Fines: Regulatory bodies impose substantial fines for non-compliance with food safety standards. These financial penalties can significantly impact a company’s profitability and operational budget.
Shutdowns: In cases of severe or repeated non-compliance, regulatory authorities may mandate temporary or permanent shutdowns of production facilities. Such shutdowns disrupt operations, leading to loss of revenue and potential damage to supply chains.
Product Recalls: Contaminated products resulting from passbox failures necessitate costly and damaging product recalls. Recalls not only lead to direct financial losses but also erode consumer trust and brand reputation.
2. Reputation and Consumer Trust
Beyond financial penalties, non-compliance has profound implications for a manufacturer’s reputation and consumer trust.
Brand Integrity: Repeated instances of non-compliance and contamination incidents tarnish a brand’s image, making it difficult to regain consumer confidence. A damaged reputation can lead to decreased market share and long-term business decline.
Consumer Trust: Consumers rely on food manufacturers to provide safe and high-quality products. Non-compliance undermines this trust, leading to negative perceptions and reduced consumer loyalty. In today’s information-rich environment, negative publicity can spread rapidly, exacerbating reputational damage.
Competitive Disadvantage: Manufacturers that fail to comply with regulatory standards fall behind competitors who prioritize food safety and quality. This competitive disadvantage can result in lost business opportunities and diminished standing in the industry.
V. Implementation Strategies for Customized Passbox
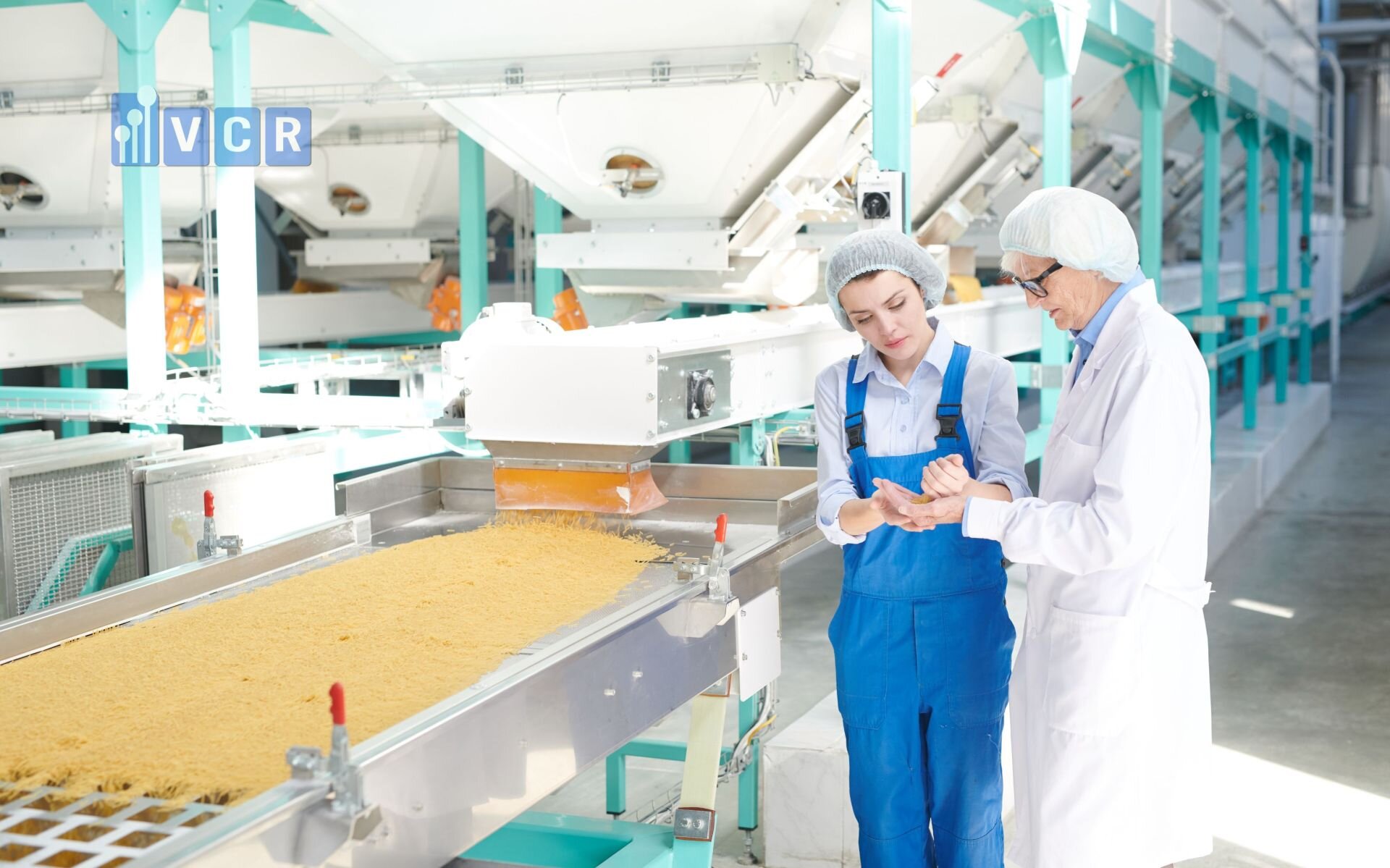
Implementing customized passboxes in specialized food manufacturing processes requires a strategic approach that ensures seamless integration, operational efficiency, and adherence to stringent safety standards. Effective implementation involves thorough needs assessment, collaboration with experienced designers and manufacturers, meticulous installation and integration, and comprehensive training and Standard Operating Procedure (SOP) development. This section outlines the key strategies for successfully implementing customized passboxes in food manufacturing environments.
A. Needs Assessment and Process Mapping
1. Identifying Specific Requirements
The foundation of successful passbox customization lies in accurately identifying the specific requirements of the manufacturing processes. This begins with a detailed analysis of existing operations to understand the unique challenges and contamination risks associated with different production lines.
Analyzing Manufacturing Processes: Conduct a comprehensive review of all manufacturing processes to determine where passboxes are needed. This involves mapping out critical points where materials are transferred between different areas, such as raw ingredient handling, packaging, and finished product storage.
Customization Needs: Identify the specific features required for each passbox based on the type of food products being handled. For example, passboxes used in allergen-controlled zones must include dedicated features to prevent cross-contamination, while those in high-humidity areas require materials and sealing mechanisms resistant to moisture.
Regulatory and Compliance Requirements: Consider regulatory standards and industry best practices that influence passbox design. Ensuring that passboxes meet food safety regulations, such as FDA’s FSMA and HACCP guidelines, is crucial for maintaining compliance and avoiding potential penalties.
2. Process Flow Analysis
Once the specific requirements are identified, the next step is to analyze the process flow to determine the optimal placement and integration of passboxes within the manufacturing environment.
Mapping Material Transfer Points: Create detailed process flow diagrams that highlight all material transfer points. This visualization helps in pinpointing where passboxes will be most effective in maintaining contamination control and operational efficiency.
Seamless Integration: Design passboxes to integrate seamlessly with existing workflows. This means ensuring that the placement of passboxes does not disrupt the flow of materials or impede worker movement. Instead, passboxes should enhance efficiency by providing controlled transfer points that streamline operations.
Space Optimization: Assess the available space to ensure that passboxes fit within the existing layout without causing congestion. Modular passbox designs can offer flexibility, allowing adjustments as manufacturing processes evolve or expand.
B. Collaboration with Designers and Manufacturers
1. Engaging with Specialized Vendors
Partnering with specialized vendors who have expertise in customized passbox solutions is essential for achieving optimal design and functionality.
Selecting Experienced Partners: Choose vendors with a proven track record in designing and manufacturing customized passboxes for the food industry. Their experience ensures that they understand the unique requirements and can offer innovative solutions tailored to specific needs.
Technical Expertise: Collaborate with vendors who possess in-depth technical knowledge of materials, airflow systems, and contamination control technologies. Their expertise is invaluable in addressing complex challenges and implementing advanced features such as automated controls and integrated sanitization systems.
Vendor Support and Services: Ensure that the chosen vendors provide comprehensive support, including design consultations, installation services, and ongoing maintenance. Reliable vendor support is crucial for the long-term success and sustainability of the customized passboxes.
2. Iterative Design and Feedback Loops
The design process should be iterative, involving continuous testing and refinement based on feedback from all stakeholders.
Prototyping: Develop prototypes of the customized passboxes to evaluate their performance in real-world conditions. Prototyping allows for the identification and resolution of design flaws before full-scale implementation.
Testing and Validation: Conduct rigorous testing to assess the effectiveness of the passbox designs in controlling contamination and maintaining operational efficiency. This includes testing airflow patterns, sealing mechanisms, and integration with existing systems.
Refining Designs: Gather feedback from operators, quality assurance teams, and maintenance personnel to refine the passbox designs. Iterative improvements ensure that the final product meets all functional and regulatory requirements while addressing any practical challenges encountered during testing.
C. Installation and Integration
1. Site Preparation
Proper site preparation is critical for the successful installation of customized passboxes.
Infrastructure Modifications: Modify existing infrastructure as needed to accommodate the customized passboxes. This may involve reinforcing walls, adjusting HVAC systems, or installing additional electrical and plumbing connections.
Compliance with Building Codes: Ensure that all modifications comply with local building codes and safety regulations. This includes obtaining necessary permits and inspections to verify that the installation meets all regulatory standards.
Environmental Controls: Implement necessary environmental controls, such as temperature and humidity regulation, to create optimal conditions for passbox operation. Proper site preparation ensures that passboxes function effectively from the outset.
2. Seamless Integration with Existing Systems

Integrating passboxes with existing systems is essential for maintaining overall operational efficiency and contamination control.
HVAC Integration: Coordinate the passbox design with the facility’s HVAC systems to ensure consistent airflow and pressure differentials. Proper integration helps maintain cleanroom conditions and prevents the ingress of contaminants.
Automation Systems: Integrate passboxes with existing automation systems to enhance functionality. This includes connecting passboxes to Supervisory Control and Data Acquisition (SCADA) systems for real-time monitoring and control.
Workflow Processes: Align passbox placement and operation with existing workflow processes to minimize disruptions. Seamless integration ensures that material transfers are efficient and do not create bottlenecks in production.
D. Training and SOP Development
1. Comprehensive Staff Training
Effective operation and maintenance of customized passboxes require comprehensive training for all relevant personnel.
Operating Procedures: Train staff on the correct use of passboxes, including opening and closing protocols, material handling techniques, and adherence to hygiene standards. Proper training minimizes the risk of contamination and operational errors.
Maintenance Protocols: Educate maintenance teams on routine maintenance tasks, such as cleaning, filter replacement, and system inspections. Regular maintenance ensures that passboxes remain in optimal working condition and prolongs their lifespan.
Emergency Responses: Prepare staff to respond effectively to emergencies, such as passbox malfunctions or contamination incidents. Training should include procedures for shutting down passboxes, containing spills, and reporting issues to management.
2. Developing Standard Operating Procedures (SOPs)
Standard Operating Procedures (SOPs) provide detailed guidelines for the consistent and safe operation of passboxes.
Daily Operations: Outline step-by-step instructions for daily operations, including material transfers, cleaning routines, and monitoring tasks. Clear SOPs ensure that all staff perform tasks uniformly and adhere to best practices.
Cleaning and Sanitization: Develop SOPs for cleaning and sanitizing passboxes to prevent microbial growth and contamination. These procedures should specify the cleaning agents, tools, and techniques to be used, ensuring thorough and effective sanitation.
Troubleshooting: Include troubleshooting guidelines in SOPs to help staff identify and resolve common passbox issues. Providing clear instructions for addressing problems minimizes downtime and maintains operational continuity.
Documentation Practices: Establish protocols for documenting passbox operations, maintenance activities, and any deviations from standard procedures. Proper documentation supports traceability, accountability, and regulatory compliance.
VI. Maintenance and Validation of Customized Passbox
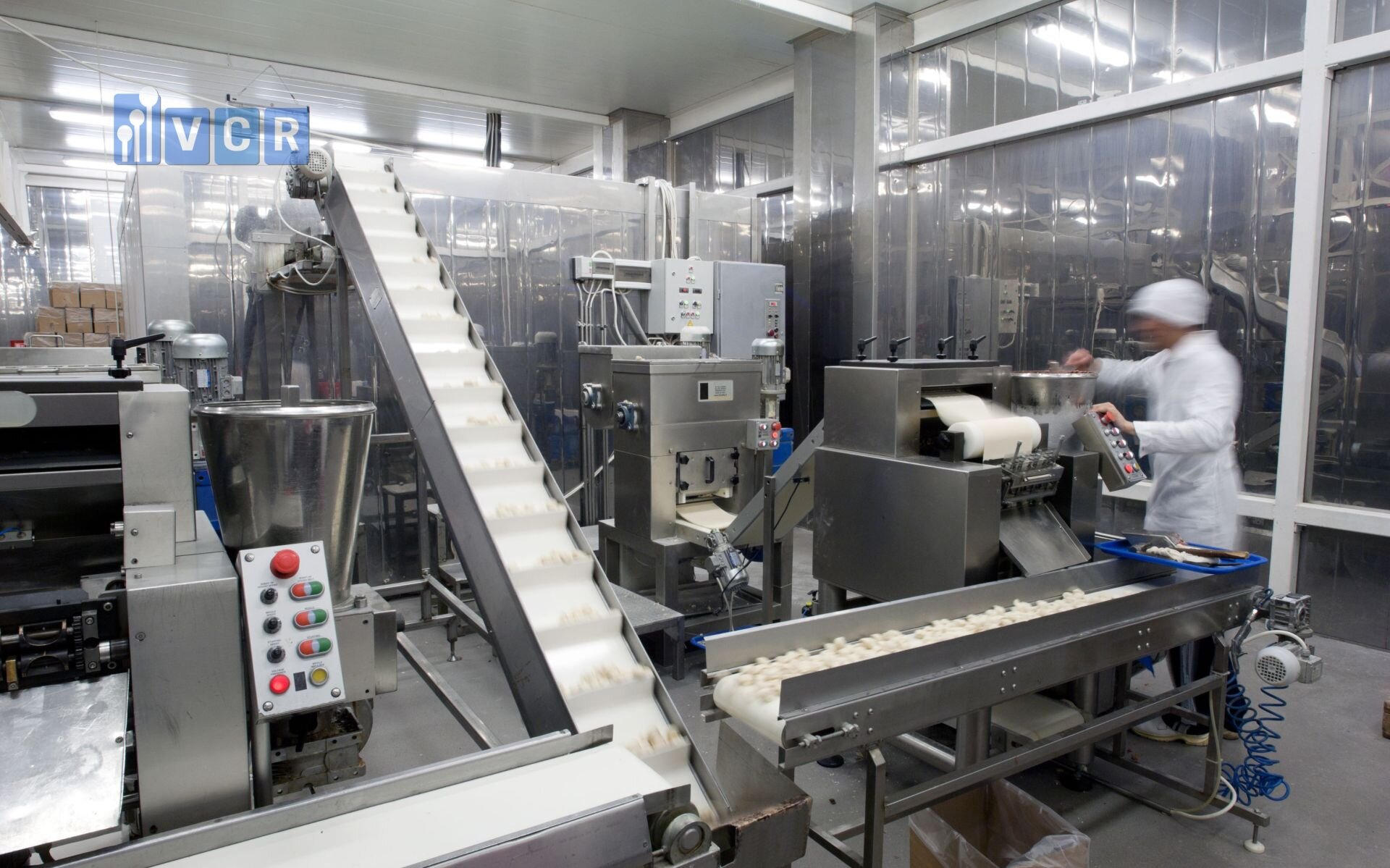
Maintaining and validating customized passboxes is essential to ensure their ongoing effectiveness in controlling contamination, preserving hygiene standards, and sustaining operational efficiency in specialized food manufacturing processes. Proper maintenance extends the lifespan of passboxes, while rigorous validation guarantees that they continue to perform as intended, even as manufacturing processes evolve. This section explores routine maintenance practices, ongoing validation and requalification, troubleshooting common issues, and the critical documentation required to support these activities.
A. Routine Maintenance Practices
1. Scheduled Inspections and Cleaning
Routine maintenance is the cornerstone of ensuring the longevity and optimal performance of customized passboxes. Scheduled inspections and cleaning are preventive measures designed to identify and address potential issues before they escalate into significant problems.
Preventive Maintenance: Establishing a preventive maintenance schedule involves regular inspections and cleaning routines based on manufacturer recommendations and industry best practices. These schedules typically include daily, weekly, monthly, and annual tasks that ensure the passbox remains in pristine condition. Regular inspections help detect early signs of wear and tear, such as minor cracks, loose fittings, or buildup of contaminants, allowing for timely interventions.
Cleaning Protocols: Thorough cleaning of passboxes is crucial to prevent microbial growth and contamination. Cleaning protocols should specify the cleaning agents, tools, and techniques to be used. For instance, using food-grade sanitizers and non-abrasive cleaning tools ensures that surfaces remain hygienic without causing damage to the passbox materials. Automated cleaning systems, such as Clean-In-Place (CIP) technologies, can be integrated into passbox designs to facilitate efficient and consistent sanitation processes.
Inspection Checklists: Utilizing detailed inspection checklists during maintenance visits ensures that no aspect of the passbox is overlooked. These checklists should cover all critical components, including door seals, airflow systems, sensors, and structural integrity, providing a systematic approach to maintenance.
2. Component Replacement
Over time, certain components of passboxes may degrade or wear out, necessitating their timely replacement to maintain functionality and hygiene.
Filters: HEPA and other high-efficiency filters are vital for maintaining clean airflow within passboxes. Filters should be replaced according to a predetermined schedule or based on performance indicators such as pressure drop measurements. Regular replacement ensures that particulate matter and microbial contaminants are effectively captured, preventing their accumulation within the passbox environment.
Seals and Gaskets: Door seals and gaskets are critical for maintaining airtight conditions and pressure differentials. These components are subject to continuous stress from door operations and environmental factors. Inspecting seals for signs of wear, brittleness, or deformation is essential, and replacing them promptly prevents air leaks and contamination ingress.
Mechanical Parts: Components such as door hinges, automated actuators, and ventilation fans may experience mechanical wear over time. Regularly assessing the condition of these parts and replacing them as needed ensures smooth and reliable operation of the passbox.
Sensors and Controls: Accurate sensors are essential for monitoring critical parameters like airflow, pressure, and humidity. Periodic calibration and replacement of faulty sensors maintain the integrity of real-time monitoring systems, ensuring that any deviations are promptly detected and addressed.
B. Ongoing Validation and Requalification
1. Periodic Performance Testing
Ongoing validation through periodic performance testing ensures that passboxes continue to operate within defined specifications, maintaining their effectiveness in contamination control.
Regular IQ, OQ, PQ Updates: Installation Qualification (IQ), Operational Qualification (OQ), and Performance Qualification (PQ) should be revisited periodically to confirm that passboxes remain compliant with design and operational standards. These updates involve re-assessing installation accuracy, operational functionality, and performance consistency under current manufacturing conditions.
Performance Metrics: Key performance metrics such as airflow velocity, pressure differentials, recovery times, and particle counts should be regularly measured and compared against established acceptance criteria. Consistent monitoring of these metrics ensures that passboxes function as intended and continue to meet hygiene and safety standards.
Validation Schedule: Developing a structured validation schedule that aligns with maintenance routines and production cycles ensures that performance testing is conducted systematically. This proactive approach helps identify and rectify performance deviations before they impact product quality or compliance.
2. Impact of Process Changes
Manufacturing processes are dynamic and may undergo changes due to product variations, scaling operations, or adopting new technologies. These changes can impact the performance and requirements of passboxes, necessitating revalidation.
Process Alterations: Any significant change in the manufacturing process, such as introducing new ingredients, altering production volumes, or modifying material transfer protocols, should trigger a revalidation of passboxes. This ensures that passboxes continue to meet the updated operational demands and maintain contamination control.
Revalidation Procedures: Revalidating passboxes involves conducting a thorough review of the changes and their potential impact on passbox performance. This may include additional IQ checks to verify installation integrity, OQ tests to assess operational functionality under new conditions, and PQ evaluations to confirm sustained performance in the revised process environment.
Documentation and Approval: All process changes and subsequent revalidation activities must be meticulously documented and approved through the appropriate quality management channels. This ensures traceability and accountability, supporting continuous compliance and operational reliability.
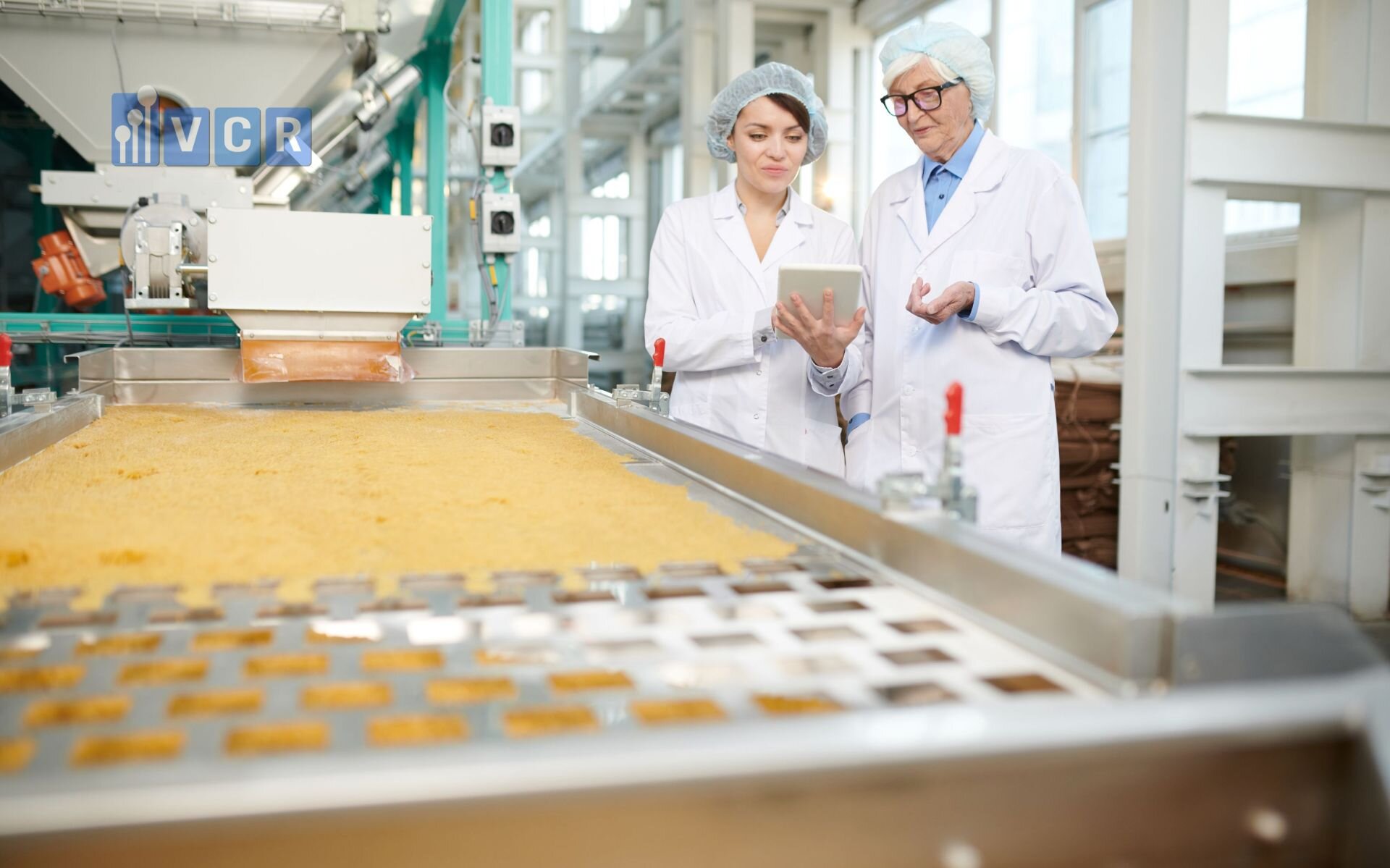
C. Troubleshooting Common Issues
Despite robust design and maintenance practices, passboxes may encounter operational issues that require prompt diagnosis and resolution to maintain their effectiveness.
1. Diagnosing Airflow Problems
Airflow issues can compromise contamination control and operational efficiency. Diagnosing and resolving these problems involves:
Identifying Blockages: Blockages in airflow pathways, such as clogged filters or obstructed vents, reduce airflow efficiency and can lead to pressure imbalances. Regular inspection and cleaning of filters and vents help prevent blockages.
Assessing Fan Performance: Ventilation fans play a crucial role in maintaining airflow. Reduced fan performance due to mechanical wear or electrical issues can impair passbox functionality. Testing fan speeds and checking for unusual noises or vibrations can help identify performance degradation.
Calibrating Airflow Sensors: Inaccurate airflow measurements due to sensor drift or calibration errors can lead to incorrect assessments of passbox performance. Regular calibration of airflow sensors ensures accurate data collection and reliable monitoring.
Resolving Airflow Inefficiencies: Once blockages or mechanical issues are identified, appropriate corrective actions such as cleaning, repairing, or replacing components must be undertaken to restore proper airflow.
2. Addressing Sealing Failures
Sealing failures can lead to air leaks and contamination ingress, undermining the passbox’s role in maintaining controlled environments.
Detecting Leaks: Visual inspections and pressure testing can help identify leaks in door seals or gasket connections. Signs of sealing failures include visible gaps, deteriorated seal materials, or unexpected pressure fluctuations.
Repairing Seals: Minor leaks can often be repaired by replacing damaged seals or reapplying sealing materials. In cases of extensive damage, replacing entire gasket assemblies may be necessary.
Ensuring Airtight Integrity: After repairs, conducting pressure tests and airflow measurements ensures that sealing integrity has been restored. Continuous monitoring helps detect any recurring sealing issues promptly.
Preventive Measures: Implementing preventive measures such as using high-quality seal materials, avoiding excessive door force, and conducting regular seal inspections can minimize the risk of sealing failures.
D. Documentation for Maintenance and Validation
Accurate and comprehensive documentation is vital for tracking maintenance activities, ensuring compliance, and facilitating audits and inspections.
1. Maintenance Logs
Maintaining detailed maintenance logs provides a clear record of all activities performed on passboxes, including inspections, cleaning, component replacements, and repairs.
Recording Activities: Each maintenance activity should be documented with details such as the date, description of the task, components involved, and the personnel responsible. This ensures traceability and accountability for all maintenance actions.
Tracking Component Changes: Recording the replacement of components like filters, seals, and sensors helps monitor the passbox’s condition over time. This information is crucial for identifying patterns of wear and predicting future maintenance needs.
Scheduling Maintenance: Documentation should include schedules for upcoming maintenance tasks, ensuring that preventive measures are consistently applied and no critical activities are overlooked.
2. Validation Reports
Comprehensive validation reports document the results of validation tests and assessments, providing evidence that passboxes continue to meet operational and regulatory standards.
Detailing Test Outcomes: Validation reports should include detailed descriptions of all tests conducted during IQ, OQ, and PQ phases, along with the results and any deviations from acceptance criteria. This provides a transparent record of passbox performance and compliance.
Assessing Compliance: Reports should evaluate whether passboxes meet all design specifications and regulatory requirements based on test outcomes. Any non-compliance issues should be clearly identified and addressed through corrective actions.
Supporting Continuous Improvement: Validation reports serve as a foundation for continuous improvement initiatives, highlighting areas where passbox performance can be enhanced and informing future design or operational modifications.
Facilitating Audits and Inspections: Well-documented validation reports streamline the audit and inspection process by providing auditors with clear, organized evidence of compliance and operational integrity. This reduces the risk of regulatory penalties and enhances the manufacturer’s credibility.
VCR is a premier manufacturer of customized passboxes based in Vietnam, dedicated to delivering advanced contamination control solutions for the food manufacturing industry. With extensive expertise and a team of skilled engineers, VCR designs and produces high-quality passboxes tailored to meet the unique hygiene and safety requirements of specialized food processing environments. Our passboxes are constructed from durable, hygienic materials and feature state-of-the-art technologies such as automated door controls, HEPA filtration systems, and integrated sanitization processes to ensure seamless and safe material transfers. Committed to excellence and regulatory compliance, VCR partners with food manufacturing engineers, quality assurance professionals, and facility designers to provide solutions that enhance operational efficiency and maintain product integrity.
For more information or to discuss your specific needs, please contact us:
Email: [email protected]
Website: vietnamcleanroom.com